Introduction to Mirrors
Predating even crude lenses, mirrors are perhaps the oldest optical element utilized by man to harness the power of light. Prehistoric cave dwellers were no doubt mesmerized by their reflections in undisturbed ponds and other bodies of water, but the earliest man-made mirrors were not discovered until Egyptian pyramidal artifacts dating back to around 1900 BC were examined. Mirrors made during the Greco-Roman period and the Middle Ages consisted of highly polished metals, such as bronze, tin, or silver, fashioned into slightly convex disks, which served mankind for over a millennium.
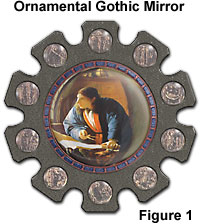
It was not until the late Twelfth or early Thirteenth Centuries that the use of glass with a metallic backing was developed to produce looking glasses, but refinement of this technique took an additional several hundred years. By the Sixteenth Century, Venetian craftsmen were fabricating handsome mirrors fashioned from a sheet of flat glass coated with a thin layer of mercury-tin amalgam (see Figure 1 for a Gothic version). Over the next few hundred years, German and French specialists developed mirror-making into a fine art, and exquisitely crafted mirrors decorated the halls, dining, living, and bedrooms of the European aristocracy.
Finally, in the mid-1800s, German organic chemist Justus von Liebig devised a method for depositing metallic silver onto a pre-etched glass surface by chemically reducing an aqueous solution of silver nitrate. This discovery was a significant advance in technology for an already well-established mirror industry, and heralded a new era in which mirrors could be produced from anything made with glass. Modern household and commercial mirrors have advanced a step further, and are usually made by sputtering a thin layer of aluminum or silver onto the back of a glass plate while enclosed in a vacuum. Scientific and optical instruments require more sophisticated fabrication techniques that include multi-layer vacuum deposition of thin films, specialized substrate materials, highly accurate polishing to extremely fine tolerances, and abrasion resistant protective coatings.
Reflection of light is an inherent and important fundamental property of mirrors, and is quantitatively gauged by the ratio between the amount of light reflected from the surface and that incident upon the surface, a term known as reflectivity. Mirrors of different design and construction vary widely in their reflectivity, from nearly 100 percent for highly-polished mirrors coated with metals that reflect visible and infrared wavelengths, to nearly zero for strongly absorbing materials.
The images formed by a mirror are either real or virtual, depending upon the proximity of the object to the mirror, and can be accurately predicted with respect to size and location from calculations based on the geometry of any particular mirror. Real images are formed when the incident and reflected rays intersect in front of the mirror, whereas virtual images occur at points where extensions from incident and reflected rays converge behind the mirror. Planar (flat) mirrors produce virtual images because the focal point, at which extensions from all incident light rays intersect, is positioned behind the reflective surface.
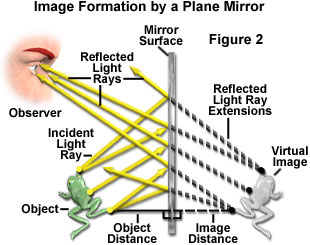
Either the front or rear surface of a planar mirror can be coated with a suitable reflective material. Common household mirrors are coated on the rear surface so that the reflective surface is protected by glass, but mirrors designed for critical scientific applications and optical systems are usually coated on the front surface, and are termed first surface mirrors. The imaging characteristics of a planar mirror can be determined by examining the position and distance of the object from the mirror surface (see Figure 2). For all planar mirrors, the object and virtual image are positioned equal distances from the reflecting surface, with individual light rays obeying the Law of Reflection (incident and reflecting rays impact and emerge at equal angles from the optical axis). The image produced by a plane mirror appears equal in size to the object, and is erect (right side up). Interior decorators often utilize the optical properties of plane mirrors to create the illusion that a room is twice its actual size.
As illustrated in Figure 2, an observer visualizes an object reflected by the mirror to be positioned behind the mirror, because the eye interpolates the reflected light rays along straight lines to the point of convergence. The only change in the object, which is evident by examining the reflection, is a 180-degree rotation around the plane of the mirror, an effect commonly referred to as reversion of the image. Thus, the mirror image of an asymmetrical object, such as a human hand, will be reversed (in effect, the mirror image of the left hand will appear as the right hand). The conversion of a right-handed coordinate system into a left-handed system in the object space is known as inversion, and multiple planar mirrors can be employed to produce an even or odd number of inversions.
In order to reflect light waves with high efficiency, the surface of a mirror must be perfectly smooth over a long range, with imperfections that are much smaller than the wavelength of light being reflected. This requirement applies regardless of the shape of the mirror, which can be irregular or curved, in addition to the planar mirror surfaces commonly seen in households. Curved mirrors are roughly divided into two categories, concave and convex, terms that are also used to describe the geometry of simple thin lenses. With mirrors, the curved surface is referred to as either concave or convex depending upon whether the center of curvature occurs on the side of the reflecting surface or the opposite side.
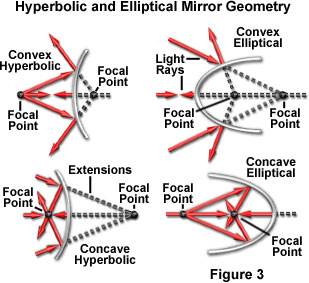
Although a majority of curved mirrors are shaped as a portion of the surface of a sphere, the surface can also be cylindrical, paraboloidal, ellipsoidal, hyperboloidal (see Figure 3), or some other form having aspherical geometry. In general, spherical mirrors produce either magnified or reduced images, depending upon whether they are concave or convex. As an example, convex rearview mirrors in automobiles produce panoramic images of reduced size, while concave shaving mirrors enlarge features of the face around the chin. Cylindrical mirrors reflect light rays into a linear focal plane on a single axis having reduced lateral dimensions, and an ellipsoidal mirror, which has two focal points and is useful as a reflector, will focus light from one focal point to the other. In contrast, a paraboloidal mirror (analogous to other aspherical examples) can focus a parallel beam of light into a point source, or vice versa, whereas hyperboloidal mirrors produce virtual images from objects positioned at the focal point. Other mirror shapes, including rod and conical, are utilized for 360-degree illumination, to bend image paths, and for laser applications. These mirrors typically have smaller diameters, rendering them ideal for use in devices with size limitations, such as fiberscopes and endoscopes. Many of the aspherical mirror geometries are difficult to manufacture with precise tolerances and possess greater degrees of aberration, resulting in higher cost and consequently, fewer practical applications.
Spherical Mirrors
Mirrors having a spherical reflecting surface are capable of forming images in a manner similar to a thin lens or a single refracting surface, but without the accompanying chromatic aberration that often accompanies lens dispersion. For this reason, mirrors are occasionally employed in place of lenses in complex optical instruments, but they cannot replace lens elements entirely because other mirror aberrations are more difficult, if not impossible, to correct. The geometric optical description for mirrors is quantitatively less complex than it is for lenses, and the two have many characteristics in common. Spherical mirrors have a well-defined radius of curvature that extends from the center of the sphere and forms right angles with every point on the surface. In addition, a line drawn from a central point on the spherical surface through the center of curvature defines the principal or optical axis of the mirror.
In the case of paraxial rays incident on a spherical mirror surface (those traveling parallel to the optical axis), all reflected rays (or their extensions) will converge at a common focal point, positioned either in front or in back of the mirror. The distance between the focal point and the mirror surface is termed the focal length of the mirror. To maintain consistency with the terminology adapted for lenses, the focal length of a concave mirror has a positive value, while that for a convex mirror is negative. As a result, mirrors that converge light rays have a positive focal length (similar to lenses) and those that diverge light rays have a negative focal length. Also, in a manner consistent with lens terminology, a transverse plane passing through the focal point is termed the focal plane, and parallel rays reflected at any angle with respect to the optical axis converge at some focal point within the focal plane.
Concave Spherical Mirrors

Explore how moving an object farther away from the center of curvature affects the size of the real image formed by a concave mirror. Also examined are the effects of moving the object closer to the mirror, first between the center of curvature and the focal point, and then between the focal point and the mirror surface.
Start Tutorial »The location of images produced by spherical mirrors can be determined experimentally, graphically, or through applying geometric formulas. Graphical or ray tracing techniques represent an easy and popular method for determining the position of images formed by a mirror. Presented in Figure 4 are parallel-ray traces indicating the principal rays and location of an image formed by a concave (Figure 4(a)) and a convex (Figure 4(b)) mirror. Principal rays are useful because they can be drawn to connect critical locations between the object, image, mirror surface, center of curvature, and the focal points without precise angle measurements.
The red, yellow and blue light rays emanating from the uppermost point of an object (P; at the green arrow tip) all reflect from the surface of the concave mirror in Figure 4(a) and are brought into focus at the conjugate point (P') to form a real, inverted image that is smaller than the object. The blue light ray travels parallel to the optical axis and is reflected through the focal point (F) before reaching the conjugate plane (the image). The red ray passes through the focal point and is reflected in a direction parallel to the optical axis by the mirror. The last principal ray, which is yellow in color, first passes through the mirror center of curvature and strikes the mirror at an angle perpendicular to the surface before reflecting back on itself. As in the case of simple thin lens ray trace diagrams, any two of these three principal rays can be utilized to locate the image, which appears at the convergence point. The third ray is then useful for confirmation of the ray-tracing scheme.
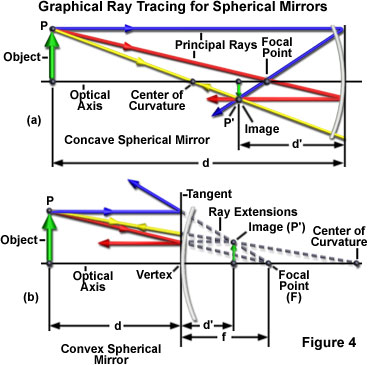
Ray traces for a convex mirror are illustrated in Figure 4(b), having the same color scheme as that employed in Figure 4(a). Light rays emanating from the green arrow tip (point P) and reflected by the mirror surface, produce extensions that diverge from the conjugate point (P') to form an upright, virtual image behind the mirror. In a manner similar to that in the concave mirror diagram, the blue light ray travels parallel to the optical axis of the convex mirror, but is now reflected at a divergent angle as if it originated from the focal point (F). An extension of the blue ray drawn through the mirror passes through the focal point. Likewise, the yellow light ray strikes the mirror at a perpendicular angle and is reflected back onto itself, but produces an extension that intersects the mirror center of curvature. The red ray, traveling at an angle to the optical axis before encountering the mirror, is reflected parallel to the axis and also produces an extension that passes through the focal point.
In review of mirror ray tracing techniques, a light ray from the object that is parallel to the optical axis is reflected through the focal point, and off-axis rays passing through the principal focal point are reflected parallel to the optical axis. Additionally, a ray striking the vertex is reflected at an equal angle from the optical axis (not illustrated), and light rays passing through the center of curvature are reflected back onto themselves. As discussed above, only two of the principal rays are necessary to reveal the geometrical parameters of an image. Mirror equations may be derived by examining the corresponding lens formulas and making several assumptions about refractive index and thickness. The most fundamental equation is termed the mirror formula and is given by the relation:
where d(0) is the distance of the object from the mirror surface, d(1) is the distance between the image and the mirror, and f is the mirror focal length. As with lenses, the focal length is positive for converging (concave) mirrors and negative for diverging (convex) mirrors. When incorporated into optical systems, the spherical shape of concave and convex mirrors enables them to act as positive and negative lenses, respectively.
The size of an image formed by a convex spherical mirror is dependent on the location of the object in relation to the focal point of the mirror, but the images are always virtual, upright, and smaller than the object. In contrast, an object positioned beyond the center of curvature in a concave spherical mirror forms a real image between the focal point and the center of curvature. When the object is moved to coincide with the center of curvature, the concave mirror forms a real image that equals the object in size, but is inverted. Moved even closer to the surface, the object forms an image that is inverted and larger than itself. At a point halfway between the mirror and its center of curvature (the focal point of the mirror), reflected light rays from the object become parallel and no image is formed (the mirror is filled with an unrecognizable blur). If the object is moved still closer, between the focal point and the mirror surface, the reflected rays diverge and form an upright, virtual image that is larger than the object. Finally, when the object rests against the surface of the mirror, the virtual image once again becomes the same size as the object.
Convex Spherical Mirrors

Discover how moving the object farther away from the surface of a convex spherical mirror affects the size of the virtual image formed behind the mirror.
Start Tutorial »Mirror ray trace diagrams, such as the examples presented in Figure 4, are specifically designed to follow the same conventions utilized for simple thin lenses. For instance, distances measured from left to right are positive, and vice versa. The incident light rays are drawn so they travel from left to right, while reflected rays travel from right to left. A line perpendicular to the optical axis and tangent to the center of the reflecting surface (termed the vertex) can be drawn as a reference from which to measure image, object, focal point, and curvature distances. By following these basic rules, the optical parameters for most mirrors can be determined and related to those of lens elements that might share duties in an optical system.
A majority of the aspherical mirror designs behave similarly to simple convex and concave mirrors when light rays near the paraxial region (close to the optical axis) are considered. In fact, many mirror shapes can be considered essentially indistinguishable from spherical mirrors in this regard. However, as light rays farther removed from the central axis are examined, deviations begin to occur and new, more specific, geometrical relationships exist between the object, image, and focal points. In addition, the magnitude and severity of optical aberrations often differ from one mirror design to another, and these must be taken into account when designing optical systems utilizing these mirrors.
Mirror Fabrication and Coating Technology
The reflectivity of any uncoated surface depends on the refractive index, angle of incidence, polarization state of incident light, and the surface quality of the material being utilized. Ideal substrates for producing low-cost mirrors include Pyrex, an economical borosilicate glass formulation that exhibits a low thermal expansion coefficient and relatively low optical deformation. Fused silica is a synthetic formulation, often employed to build rugged laser mirrors, that features excellent thermal stability, broadband wavelength transmission, and can be polished to extremely close tolerances in order to minimize wavefront distortion and light scatter. In addition, a glass ceramic developed by Schott Research Laboratories, Zerodur, possesses characteristics that render this material an excellent candidate for high-quality mirror fabrication. The ceramic is transparent, but has a slightly yellow cast and features extremely low thermal expansion. Other materials, such as infrared-transparent calcium fluoride, are useful in producing critical mirrors for high-energy laser systems.
The quality (smoothness) and flatness of optical surfaces is one of the primary factors to consider when designing mirrors for specific applications. When a plane wavefront is reflected from a mirror surface, the actual distortion produced in the wave can range from one-half to twice the value of the surface flatness. Substrate deviations from a perfect plane are usually expressed in terms of how many imperfections in the size range of visible light wavelengths (550 nanometers), or wavelength fractions, can be detected across the surface. Many non-critical applications will support large deviations of one or more wavelengths, while more stringent applications often require the surface to deviate no more than a quarter wavelength or less. Mirror surface smoothness is determined by measuring the number of scratches and digs per unit area and expressing this value as a ratio. Thus, a scratch/dig ratio of 70/40 is suitable for low-end applications, while a ratio of 10/5 is required for high-performance laser systems and analytical optical imaging applications where wavefront distortion must be held to a minimum.
The ability of a mirror to conduct heat is also important for many applications. Metallic mirror substrates can conduct heat away from optical systems more efficiently than glass, but they are often more difficult to fabricate in specialized geometries and usually add excess weight to the system. Lightweight metals, such as beryllium, are becoming popular with designers and can be utilized in critical situations where heat is an issue and stiff mirrors are required. Many of the newer glass formulations feature excellent thermal expansion coefficients and are suitable for applications that do not suffer from excessive heat problems.
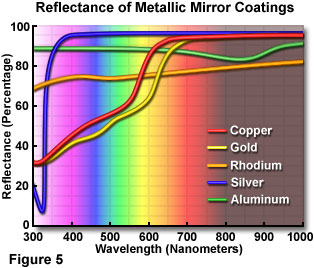
The simplest and most common mechanism utilized to produce mirror coatings is to apply a thin layer of metal to a polished glass substrate by vacuum deposition techniques. Metals of choice (see Figure 5) include silver, aluminum, copper, gold, and rhodium. In general, a 100-nanometer layer of aluminum or silver provides an excellent coating for a variety of applications, but thicker coatings result in rougher surfaces that increase light scatter. Aluminum can be applied directly to glass, but chrome or other intermediary layers must be utilized for gold and other metals. A freshly deposited aluminum coating displays a reflectance of about 90 percent over the most of the ultraviolet, visible, and near-infrared spectral regions (Figure 5), while silver produces a corresponding reflectance of about 95 percent in the visible and infrared, but drops severely in the ultraviolet. The reflectance of a metallic mirror can be calculated according to the following equation:
where (n) is the refractive index of the metallic coating and k is the molar extinction coefficient. In general, as the reflected wavelength value increases (into the infrared region) the refractive index and extinction coefficient also increase, leading to increased reflectance. Silver is one of the most suitable materials for mirrors designed to reflect light in the visible region, but aluminum is more efficient for ultraviolet light. However, as wavelengths are increased into the infrared region, the reflectance of aluminum decreases below 90 percent, which can deter performance in optical systems having several mirrors. For example, at a reflectance value of 80 percent, a system with six mirrors would have a throughput of only 26 percent. Copper and Gold are useful only in the long wavelength visible (greater than 650 nanometers) and infrared regions (see Figure 5), while rhodium can be used across all spectral regions for non-critical applications, such as household mirrors.
A serious problem in metallic mirror coatings occurs with the formation of oxides (tarnish) and other deposits when thin-films are exposed to the atmosphere, which can lead to significant degradation of mirror performance. In order to protect delicate metallic mirror coatings, the surface is usually covered with a dielectric overcoat that enables handling and cleaning of the mirror, and improves the durability while reducing oxide formation. Aluminum films can be protected by a half-wavelength thick layer of silicon monoxide to produce a relatively abrasion-resistant surface. In some cases, several dielectric layers with alternating refractive index values are deposited over aluminum films to further enhance reflectance and increase the resiliency of the overcoat. Multiply coated metallic mirrors are often referred to as enhanced reflectors, and represent the most advanced coatings in this category. Gold and silver films are also covered with single or multiple dielectric silicon monoxide coatings to produce results similar to those observed with aluminum.
Dielectric Mirror Coatings
A typical mirror having a metallic coating reflects about 90 percent of the incident light waves in the ultraviolet, visible, and infrared spectral regions. In order to improve this performance, several layers of transparent dielectric materials, such as titanium dioxide and silicon dioxide (having alternating high and low refractive indices), can be applied to a smooth substrate to produce what are known as dielectric mirrors (see Figure 6). Partial reflection of the incident light occurs at each interface between the dielectric layers to produce coherent (in phase) light waves that can be reinforced by constructive interference. The result is high-performance mirrors that can achieve reflectivities approaching 100 percent for critical imaging and laser applications. In addition, dielectric coatings are far more durable than many protected metallic coatings.

Dielectric mirrors can be fine-tuned to reflect specific wavelengths by trimming the thickness of each layer so that the product of the thickness and refractive index equals one-quarter of the target wavelength. This type of coating is termed a quarter wavelength stack reflector. In most cases, the first and last layers in a stack are made with the higher refractive index material, and internal layers are interleaved between high and low refractive indices. Increasing the number of layers can increase the reflectance for specific wavelengths, but often at the expense of spectral bandwidth. Another drawback is that dielectric mirrors are often very sensitive to the angle of incidence and can produce undesirable plane-polarized light when incorrectly positioned.
The limited reflected spectral region exhibited by dielectric mirrors generally relegates their usefulness to specific applications. A common task for these mirrors is to reflect a portion of the light spectrum passing through an optical system, while passing a selected region of wavelengths. Mirrors of this type are termed dichromatic or dichroic mirrors because they effectively separate light into two distinct spectral regions. Another popular use for dielectric mirrors is the reflection of laser beams, either as part of the laser cavity itself, or as a critical component of the train that directs the beam through an optical system. Typical dielectric mirrors intended for laser applications consist of 20 to 25 thin-film layers, which produce a maximum reflectance of greater than 99.9 percent.
Broadband dielectric mirrors can be produced by combining two quarter-wavelength stacks that have overlapping bandpass wavelength regions. These mirrors often feature up to 100 alternating dielectric layers, which significantly increase the cost and difficulty in fabrication. However, their performance is unmatched and very durable multi-layer dielectric mirrors can be produced that have more than 99 percent reflectance over the entire visible light spectrum.
Multicoated dielectric mirrors that are capable of selectively passing visible wavelengths while reflecting infrared are termed hot mirrors. These mirrors, which are typically fabricated as flat plates or concave reflectors, are very useful in projection and illumination systems that typically suffer from excessive heat generated by high-intensity lamps. The wavelength band reflected in the infrared region is increased for extended hot mirrors, a high-performance version of the standard infrared-reflecting dielectric mirror. Infrared wavelengths are often removed from an optical system in a single reflection by a hot or extended hot mirror. Alternatively, the infrared wavelengths can be diverted by a hot mirror to a region where heat dissipation is more convenient (such as a fan unit or heat sink). Related mirrors are designed to reflect visible light while transmitting infrared. Termed cold mirrors, these dielectric reflectors can be utilized to remove heat from optical systems by transferring it out through the mirror. Hot and cold mirrors are utilized in solar cells and also in the helmets and visors of space suits to protect astronauts from infrared solar radiation.
Mirror Optical Aberrations
When paraxial light rays are reflected from a spherical or aspherical mirror surface, the images produced are in sharp focus. However, light rays collected from all distributed object points and highly oblique off-axis rays often produce varying focal points (depending upon mirror geometry) that result from a number of well-documented artifacts known as optical aberrations. This phenomenon is illustrated in Figure 7 for the most common defect, spherical aberration, where parallel incident rays at increasing distances from the axis are brought into focus closer to the mirror surface. When a small screen is placed at the paraxial focal plane and then moved toward the mirror, a point is reached where the image size is focused to a minimum. This region is termed the circle of least confusion.
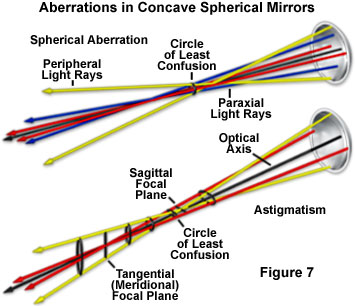
Spherical aberration can be reduced or eliminated by alterations to mirror design. For example, a parabolic mirror will produce reflection patterns similar to a concave spherical mirror, but the parabolic mirror geometry can be altered to bring all reflected rays into a common focus. Another approach involves coating the rear surface of a spherical meniscus lens and utilizing refraction of light through the glass lens element to alleviate spherical aberration. Ellipsoidal mirrors are inherently free of spherical aberration at the focal points of the ellipsoid, and the same is true for hyperboloidal mirrors.
Off-axis aberrations, such as astigmatism (Figure 7), occur when the object is positioned away from the optical axis of the mirror. Incident rays emanating from the object strike the mirror at oblique angles and result in the formation of two mutually perpendicular lines instead of an image point. Parabolic mirrors, which are free of spherical aberration, often demonstrate a significant degree of astigmatism for images positioned at locations that are far off-axis. For this reason, paraboloidal reflectors are restricted in their application to devices, such as astronomical telescopes and searchlights, which project or collect parallel light rays.
Like lenses, spherical and aspherical mirrors suffer from other common aberrations including coma, field curvature, and distortion, but they are free of chromatic aberration, one of the most serious optical defects experienced with thin lenses. This fact has been utilized to advantage by several manufacturers who have produced microscope objectives constructed from mirrors that are entirely free of chromatic aberration.
Mirror Applications
Optical microscopes make extensive use of planar mirrors, both for directing the illumination beam through the optical pathway and onto the specimen, and to project images into the eyepieces or an image sensor. Among the other applications for planar mirrors is the direction of light through pathways in simple and complex optical systems, and routine duties such as choppers, general beam deflectors, and image rotators. Elliptical flat mirrors have an elongated major axis and are employed for bending or folding light at precise angles with minimum wavefront distortion.
Cylindrical mirrors, which focus light on a single axis, are utilized as beam spreaders, line generators, and for magnifying images along one axis. In contrast, the more popular convex mirrors are seen practically everywhere, from Christmas tree ornaments to wide-angle security mirrors in department stores. Huge parabolic mirrors found in telescopes collect light from the far corners of the universe, while smaller versions broadcast light back into space in the form of searchlights. A hyperboloidal mirror design is even utilized as the primary light collector for the Hubble Space Telescope.
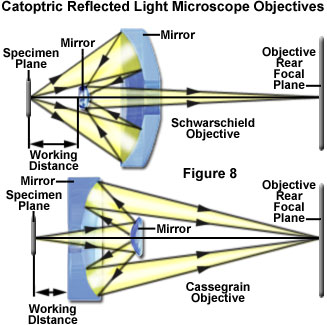
Closer to home, mirrors play an important role in specialized darkfield and reflected light microscope illumination systems. Aspherical paraboloidal mirrors are utilized to form a hollow inverted cone of illumination at high numerical aperture for darkfield imaging, while elliptical mirrors are utilized to direct light from vertical illuminators through the objective in reflected light systems. Specialized objectives, termed catoptric (see Figure 8), are employed in reflected light microscopy and have two basic advantages over their lens-based counterparts. Catoptric objectives are free of chromatic aberration and do not absorb significant amounts of ultraviolet and infrared light. The latter factor has led to the development of reflecting objectives for both ultraviolet and infrared microscopy, in addition to applications in microspectrophotometry.
Another advantage of catoptric objectives is that they can be designed and built to have much longer working distances than refracting objectives of equivalent magnification and numerical aperture. This enables the objectives to be utilized for hotstage microscopy at temperatures that would damage the front lens element of a refracting objective. In addition to catoptric objectives, mirrors play an important role in fluorescence microscopy, where they act as dichromatic beamsplitters to direct excitation wavelengths toward the specimen, and then block the same light after it has been reflected back through the objective. Other parts of the microscope also incorporate mirrors. Arc-discharge and tungsten-halogen lamphouses often have parabolic reflectors that help concentrate illumination through the collector lens and into the microscope optical pathway. In addition, confocal microscope scanning heads employ carefully orchestrated mirrors to scan a laser beam across the specimen in a raster-like pattern. These and a seemingly endless list of other simple and advanced applications make mirrors one of the most important optical components in the physicist's toolbox.